Thursday, October 22, 2015
Book Update...
My recent book has been updated. Same content, same number of pages, but structure is different. Writing this book has made me go back and recall accomplishments, failures and the struggle of being a furniture maker in today's disposable society. Received print copies this week and it looks great! There is an eBook version available at the web site also. Orders are welcome through www.woodskills.com . Updated this post with cover from new book. Below is a description of the book.
Norman Pirollo, successful founder of White
Mountain Design, White Mountain Toolworks, Refined Edge Design, WoodSkills and
Pirollo Design, chronicles his fascinating journey of transitioning from full
time employment to self-employment at woodworking. He faced many obstacles
throughout the journey and financial support was often at the forefront.
Norman narrates
his creative journey from childhood through adulthood. Perseverance, fate and
critical decisions all combined to map out the direction he followed in life.
Often seeking creativity and challenges in life, woodworking ultimately became
his creative outlet. Follow the riveting story of
how his hi-tech career gradually evolved into a successful woodworking career. He
owes a great deal to his former hi-tech career which provided him fulfillment
for a number of years. Discover how Norman acquired the skills and techniques to
be able to craft heirloom furniture today. Delving into and studying the history of furniture design has provided
him the language and background to develop his own contemporary styled
furniture. Read how he immersed himself into the contemporary furniture world
to develop a style and voice of his own. Find out how, through twists and
turns, Norman acquired the expertise and proficiency to become an award-winning
furniture maker. The opportunity to work at something he truly
enjoys has ultimately brought solace and independence to his life.
Wednesday, July 29, 2015
Latest News....
Currently working on a furniture commission for a client. There is no deadline, although this sometimes prolongs the project. A famous saying I like to quote "If it weren't for deadlines, I would never get anything done". However, I'm able to juggle the commission with another project further down, so all good!
Was informed this week that one of my furniture designs ( display cabinet) is included in the upcoming Furniture Society book "Rooted", due out in September. The book is a collaboration with Schiffer Publishing. I am invited to the book launch in September in NYC. I might just go as this is an opportunity to talk about my work with attendees.
In other news...
I've had my nose to the grinding wheel these past few weeks. Yes... writing another book and why did I decide to do this in the lazy days of summer :) In the final stages of the manuscript.. then editing, re-writing sections of it, proof-reading, etc. Planning to make an announcement about the book later in August.
The summer is quickly going by and I haven't even been on vacation yet, hopefully next week for a few days!
Was informed this week that one of my furniture designs ( display cabinet) is included in the upcoming Furniture Society book "Rooted", due out in September. The book is a collaboration with Schiffer Publishing. I am invited to the book launch in September in NYC. I might just go as this is an opportunity to talk about my work with attendees.
In other news...
I've had my nose to the grinding wheel these past few weeks. Yes... writing another book and why did I decide to do this in the lazy days of summer :) In the final stages of the manuscript.. then editing, re-writing sections of it, proof-reading, etc. Planning to make an announcement about the book later in August.
The summer is quickly going by and I haven't even been on vacation yet, hopefully next week for a few days!
Monday, June 22, 2015
Artist Talk...
I was recently contacted about giving an Artist Talk to a local arts organization. It didn't take much to convince me, especially after the organizer mentioned I would be paid a honorarium for my efforts. I then began work on developing on a comprehensive power point slide show of the evolution of my furniture, wood sculpture, and wood art. Gathering all the photos and information of a six year period was probably the largest challenge. It was then a matter of piecing everything together in chronological order with notes and talking points for each slide.
There was a period of two years where I would create elaborate scale models of furniture to determine their appeal, I enjoyed talking about this period. I have since embraced CAD design and most of my design work originates on a computer with small maquettes created afterwards. Creating the scale models of furniture, many of which became sculptural work, was a prolific, exciting time for me. I began to experiment with combining alternative mediums to wood over this two year period.
Technical considerations such as how to attach metal to wood and how to attach glass to metal came up. The issue of expansion and contraction is somewhat different with extremely stable material such as metal and glass. Metal and glass don't noticeably expand or contract with environmental changes such as wood does. Another interesting technical issue that came up was the lack of a compression characteristic in metal. The slots or holes which I use to insert metal components need to be created very precisely for precision fitting.
Working with metal also involves slightly different tools and processes. I don't even prepare the metal components in the work space I work with wood to not contaminate wood with metal filings. Once these issues were overcome, the design possibilities available to me were unlimited. The media I previously created my designs with was somewhat limited to different types of wood; domestic, exotic and figured. Today I can incorporate metal, glass and possibly stone in my work, along with my predominant medium of wood.
There was a period of two years where I would create elaborate scale models of furniture to determine their appeal, I enjoyed talking about this period. I have since embraced CAD design and most of my design work originates on a computer with small maquettes created afterwards. Creating the scale models of furniture, many of which became sculptural work, was a prolific, exciting time for me. I began to experiment with combining alternative mediums to wood over this two year period.
Working with metal also involves slightly different tools and processes. I don't even prepare the metal components in the work space I work with wood to not contaminate wood with metal filings. Once these issues were overcome, the design possibilities available to me were unlimited. The media I previously created my designs with was somewhat limited to different types of wood; domestic, exotic and figured. Today I can incorporate metal, glass and possibly stone in my work, along with my predominant medium of wood.
Friday, June 5, 2015
A Case for Dowels...
My latest book is complete and published, I can get back to woodworking now. Writing, editing, and publishing a book is such an intensive process, it demands total focus.
In many of my cabinet assemblies I use dowels to attach the sides to the top and bottom. The use of dowels gives flexibility to the design of the corner joint. For example, I can offset the side panels away from the edge of the top or bottom and in the process work the protruding edge of the top and bottom into a shaped contour,chamfer, rabbet, etc. The alternative would be to use specific corner joints which need to have the side panel and top or bottom panel intersect right at the very edge. An example of this would be a dovetailed joint, a box joint, or a rabbet and lip edge. If you've ever read up on James Krenov and his work, you will find that he embraces the dowelled corner joint for these very same reasons. This is where I received the inspiration for this type of joint and its virtues.
Creating the dowelled joint involves accurate measurement , but most importantly it involves the little jig you can see in the photo, the dowelling guide. This is a piece of wood with the exact dimensions of the panel I am dowelling, the length and thickness. The dowel holes are marked with arbitrary spacing and the dowel guide holes are bored out on the drill press. I use this dowelling guide to create the dowel holes on both of the mating surfaces, in this case the side panel and the top or bottom panel. There is some skill involved in aligning the dowelling guide to both surfaces since the holes for the dowels need to be perfectly aligned. Marking and orienting the dowelling guide to the correct edges becomes very important and I make many pencil marks in the process. The old adage, "measure twice , cut once" is better written as "measure and mark three times, drill once" for this process.
In many of my cabinet assemblies I use dowels to attach the sides to the top and bottom. The use of dowels gives flexibility to the design of the corner joint. For example, I can offset the side panels away from the edge of the top or bottom and in the process work the protruding edge of the top and bottom into a shaped contour,chamfer, rabbet, etc. The alternative would be to use specific corner joints which need to have the side panel and top or bottom panel intersect right at the very edge. An example of this would be a dovetailed joint, a box joint, or a rabbet and lip edge. If you've ever read up on James Krenov and his work, you will find that he embraces the dowelled corner joint for these very same reasons. This is where I received the inspiration for this type of joint and its virtues.
Creating the dowelled joint involves accurate measurement , but most importantly it involves the little jig you can see in the photo, the dowelling guide. This is a piece of wood with the exact dimensions of the panel I am dowelling, the length and thickness. The dowel holes are marked with arbitrary spacing and the dowel guide holes are bored out on the drill press. I use this dowelling guide to create the dowel holes on both of the mating surfaces, in this case the side panel and the top or bottom panel. There is some skill involved in aligning the dowelling guide to both surfaces since the holes for the dowels need to be perfectly aligned. Marking and orienting the dowelling guide to the correct edges becomes very important and I make many pencil marks in the process. The old adage, "measure twice , cut once" is better written as "measure and mark three times, drill once" for this process.
Thursday, May 14, 2015
Latest Book...
My latest book is now complete and off to the publisher. I will be receiving print copies next week and an eBook version will be available in a few days. Orders are welcome through www.woodskills.com . Updated this post with cover from new book. Here is part of the blurb for the book.
Norman Pirollo chronicles his fascinating journey over a 40 year period. Follow the riveting story of how his hi-tech career gradually evolved into a woodworking career. Read how Norman overcame obstacles and through determination and perseverance, finally attained his goal of self-employment at woodworking. Discover how Norman acquired the skills and techniques to be able to craft heirloom furniture today. Author Norman Pirollo shares his creative journey from childhood through adulthood. Perseverance, fate and critical decisions all combined to map out the direction he followed in life.
Norman Pirollo chronicles his fascinating journey over a 40 year period. Follow the riveting story of how his hi-tech career gradually evolved into a woodworking career. Read how Norman overcame obstacles and through determination and perseverance, finally attained his goal of self-employment at woodworking. Discover how Norman acquired the skills and techniques to be able to craft heirloom furniture today. Author Norman Pirollo shares his creative journey from childhood through adulthood. Perseverance, fate and critical decisions all combined to map out the direction he followed in life.
Thursday, May 7, 2015
Upcoming Book...
I feel like a hermit lately. My most recent project is to write another book. This book chronicles my woodworking journey over the past 30 years. As well, a considerable part of the book is devoted to the years leading up to the beginning of my woodworking. Writing the book has consumed all of my time lately as I have had to go back decades to remember every detail of my life. I am in the final stage of writing the book and it should be published in the next two weeks. I promise it to be an interesting book and a great summer read.
I finally hunkered down and dedicated myself to this in the past few weeks. Writing this book has been a dream of mine for a few years but the timing was never right. This explains why I have not had time to post much in the blog. Stay tuned for more updates on the book. Sorry no pics as I have none, but will very soon.
I finally hunkered down and dedicated myself to this in the past few weeks. Writing this book has been a dream of mine for a few years but the timing was never right. This explains why I have not had time to post much in the blog. Stay tuned for more updates on the book. Sorry no pics as I have none, but will very soon.
Sunday, April 26, 2015
Cabinet Backs...
Part of my cabinet design and build process involves the creation of a cabinet back. Conventional wisdom says the back of a cabinet is not nearly as important as the front or sides, so it merely needs a panel which is rabbeted into the sides, top and bottom. The problem with this thought process is the assumption that the back of the cabinet will be placed against a surface or wall and not seen.This doesn't apply to all cabinets as many cabinets are designed as showcase cabinets and placed away from walls; sometimes placed in the center of a room or even a foot or two away from a wall. Something also feels wrong about diminishing the importance of the back of a cabinet when so much emphasis is placed on the design and structure of the front and sides of the cabinet. With this in mind, the need for a more aesthetically pleasing cabinet back becomes important, along with the function that it introduces to the cabinet. An example of function is a wall-mounted cabinet that needs a structurally strong back.
The resulting back panel which best meets the criteria of both aesthetics and function is the frame and panel back; a panel inset into a surrounding frame composed of rails and stiles. The frame and panel back is inset into the cabinet back much like a conventional panel would but it also provides some rigidity to the cabinet. In the situations where a single panel is too wide, a middle stile is installed to divide the frame into two halves; otherwise for smaller cabinets a single panel is sufficient. The panel itself can either complement or contrast the cabinet, providing an interesting focal point once the doors of the cabinet are opened, as well as drawing the eye to the pleasing back of the cabinet.
Saturday, April 11, 2015
Hand Tool Solace...
Interesting facts about using hand tools. Hand tool
use usually requires harder physical work than power tools, but they offer a
higher degree of skill and concentration in achieving accuracy. Hand tools will
always be ensured a place in the workshop due to their compactness and relative
economy. In many cases, they provide the quickest solution since they require little or
no setup time. Some cabinet making still calls for many operations which
machines cannot tackle. The other main advantage to using hand tools is the
pure enjoyment derived from them. Hand tools operate in relative quiet,
therefore not creating the noisy distractions that power tools can sometimes
produce. Hand tools such as chisels and hand planes require sharpening
occasionally, which is another skill that needs to be developed.
Hand tools
have evolved over the past centuries, and today’s tools are vastly superior in both quality of metal, and manufacturing accuracy. The hand tools of
yesteryear remain treasured items though, since there is almost always a story
behind a particular tool. Here in my furniture studio I use hand
tools as much as possible, due to the benefits of reduced dust and noise levels
and the higher degree of fine craftsmanship possible. Most educational programs
in woodworking begin by teaching the use and virtues of hand tools. This is
done because hand tools are almost essential, and will be needed at some phase
of a project. Projects can be built exclusively with hand tools or a
combination of hand tools and machine tools.
Edge jointing and flattening a board shown above. It is not
often possible to place two pieces of gap-free wood together without using a hand
plane on their edges. Wood must be smoothed, squared up, and made to fit, the three main jobs
of a hand plane. Although machinery exists to perform these tasks, often highly figured wood surfaces need to be planed by hand to minimize tearout. I use a combination of power and hand tools to prepare board surfaces and edges. For larger boards, I typically dimension the boards using machinery to close to their final dimensions. I then tackle the boards using a series of hand planes. For smaller boards, I just use hand planes to joint and flatten the surfaces as I have more control of the process. So I often seek methods of using hand tools instead of power tools to create the components for my furniture. Why do this when machines are available? Machines are great for repeatability and production work, but to work the nuances in wood; hand tools rule!
Labels:
furniture making,
hand planes,
hand tools,
preparing wood
Friday, April 3, 2015
Mockups...
Valuable information from an earlier post on a display cabinet design. After completing the main case of a display cabinet, work began to create the inner drawer case. The first step in the sequence was to get the proportions correct using a cardboard mock up of the drawer case. After a few iterations, the mock up in the photo was the preferred layout. The design considerations which used are as follows:
A cardboard mock-up is a very important step in my opinion, as it serves to both provide a visual image of the drawer case and to point out any possible subtle issues with the layout. The drawer case is set back from the edge of the main case to allow for drawer handles and a little extra for the door stops. The drawers can be removed and individually placed on the top of the drawer case for better viewing. I debated whether to overlay the horizontal drawer dividers with the door fronts, but since all the wood is uniform and of the same species ( cherry), I would have the horizontal dividers visible. The components of the drawer case are for the most part dadoed and rabbeted together and the horizontal dividers each slide in between two grooves. The center vertical divider will be permanently attached to the drawer case. The rabbeted sides will also have a couple of dowels in each of four edges for reinforcement.
Since the cardboard mock-up is sized exactly to scale, I have the benefit of using it to size the components of the drawer case for milling and dimensioning. At this point, the boards used for the drawer case are sawn and they are allowed to stabilize before any further processing. This is to remove any inner stresses in the wood.
The individual drawers will have dovetailed drawer fronts and rabbeted backs and the bottom panel will be floating in a small groove on all four sides of the drawer.
Height of the drawer case, number of drawers, width and height of individual drawers
A cardboard mock-up is a very important step in my opinion, as it serves to both provide a visual image of the drawer case and to point out any possible subtle issues with the layout. The drawer case is set back from the edge of the main case to allow for drawer handles and a little extra for the door stops. The drawers can be removed and individually placed on the top of the drawer case for better viewing. I debated whether to overlay the horizontal drawer dividers with the door fronts, but since all the wood is uniform and of the same species ( cherry), I would have the horizontal dividers visible. The components of the drawer case are for the most part dadoed and rabbeted together and the horizontal dividers each slide in between two grooves. The center vertical divider will be permanently attached to the drawer case. The rabbeted sides will also have a couple of dowels in each of four edges for reinforcement.
Since the cardboard mock-up is sized exactly to scale, I have the benefit of using it to size the components of the drawer case for milling and dimensioning. At this point, the boards used for the drawer case are sawn and they are allowed to stabilize before any further processing. This is to remove any inner stresses in the wood.
The individual drawers will have dovetailed drawer fronts and rabbeted backs and the bottom panel will be floating in a small groove on all four sides of the drawer.
Sunday, March 29, 2015
Hand Planes...
Over the years I have amassed quite a few hand planes in my shop. The hand planes range from early wood and transitional planes to specialty rabbeting planes, block planes, bench planes and jointer sized planes. For a time, I enjoyed restoring old wood and transitional hand planes and would often re-sole the transitionals with new hardwood soles. I replaced cracked handles with newly crafted ones. I soon found that these early versions of hand planes did not perform as well as modern hand planes even with considerable fettling and tuning. For a period of time, I was crafting my own wood bodied hand planes with modern thick blade assemblies and these performed considerably better as the mouths were tighter.
On to the modern steel-bodied planes. I currently own an assortment of these hand planes primarily from two or three manufacturers and they tend to perform very well as long as the blades are kept sharp. Regular sharpening is key to the performance of a hand plane. Also, adjustments are much more precise on the newer hand planes with either Norris type or Bedrock type setups.
With the considerable assortment of hand planes in my shop, I find I that I tend to reach for the same four planes, These are a No. 4.5, No. 7, Standard angle Block and Lo-angle Block. I very often grab the Standard angle block plane as a small smoother when working on small parts. It works well, is light and easy to maneuver. The bench smoother is a Bedrock type No. 4.5 and is my most frequently used hand plane. The longer No.7 is used to work long edges and flatten boards. The Lo-angle block plane is used primarily for planing across short edges and ends of boards. I reach for some of the other specialty planes when the need arises. The conclusion to all this is that more often than not I find myself reaching for these four hand planes. It is easier to keep these hand planes blades sharp and thus maintain fewer tools. This was not planned but a method of work developed over the years for reasons of efficiency, versatility and speed.
All for now...
On to the modern steel-bodied planes. I currently own an assortment of these hand planes primarily from two or three manufacturers and they tend to perform very well as long as the blades are kept sharp. Regular sharpening is key to the performance of a hand plane. Also, adjustments are much more precise on the newer hand planes with either Norris type or Bedrock type setups.
With the considerable assortment of hand planes in my shop, I find I that I tend to reach for the same four planes, These are a No. 4.5, No. 7, Standard angle Block and Lo-angle Block. I very often grab the Standard angle block plane as a small smoother when working on small parts. It works well, is light and easy to maneuver. The bench smoother is a Bedrock type No. 4.5 and is my most frequently used hand plane. The longer No.7 is used to work long edges and flatten boards. The Lo-angle block plane is used primarily for planing across short edges and ends of boards. I reach for some of the other specialty planes when the need arises. The conclusion to all this is that more often than not I find myself reaching for these four hand planes. It is easier to keep these hand planes blades sharp and thus maintain fewer tools. This was not planned but a method of work developed over the years for reasons of efficiency, versatility and speed.
All for now...
Labels:
block plane,
hand planes,
smoother,
woodworking,
woodworking tools
Wednesday, March 25, 2015
History of Furniture Design...
It is fascinating how furniture design has evolved over the centuries. If we return to the middle ages and the era before, quite a few developments in furniture construction techniques were in progress. Prior to this era, in the centuries before, very little furniture was available. It was considered a luxury to own furniture such as chairs, tables and cabinets. The larger, more finely made furniture of this era was typically destined for the aristocracy of the time as a display of their wealth and status. Most conventional furniture of these early periods was assembled without consideration to wood expansion and contraction or wood movement. This worked for many years, since the interior of buildings in this era was often at the same temperature as the exterior. With the advent of heated interiors, wood movement became much more of a factor to deal with in construction and design of furniture, and the practice of simply assembling wood planks together to form furniture needed to evolve. It was in the middle ages that frame and panel construction was adopted. This technique allowed a solid wood panel to literally float within a wood frame composed of rails and stiles. The solid wood panel could expand and contract on a seasonal basis, and not cause any structural failure within the furniture. All of a sudden many more possibilities were created for furniture design and its widespread appeal began in earnest.
Furniture also began to become more affordable as of the 18th and 19th century, more furniture makers existed and sound construction techniques began to become standardized. There are numerous periods over the past centuries and each of these had a style or styles associated with them. Additionally, each country had a style of its own within these periods. One can see how similar furniture design principles were adopted by successive countries over the different periods. Popular furniture
styles which are widely recognized have familiar names such as English Chippendale, German Biedermeier, American Federal and Arts & Crafts, French Art Nouveau, Italian Rococo, etc.
To be continued...
Furniture also began to become more affordable as of the 18th and 19th century, more furniture makers existed and sound construction techniques began to become standardized. There are numerous periods over the past centuries and each of these had a style or styles associated with them. Additionally, each country had a style of its own within these periods. One can see how similar furniture design principles were adopted by successive countries over the different periods. Popular furniture
styles which are widely recognized have familiar names such as English Chippendale, German Biedermeier, American Federal and Arts & Crafts, French Art Nouveau, Italian Rococo, etc.
To be continued...
Saturday, March 21, 2015
Dynamic Design...
Over the past years, I have come to use a new term in my design
philosophy. The term, "dynamic design", allows me to modify a design
to adapt to circumstances, for either technical considerations, or for purely
aesthetic reasons. This is a term I have coined to describe how design doesn't
necessarily need to be cast in stone but instead can be modified as a project
progresses. The changes I refer to can be either subtle changes or large scale
changes. One of the meanings for the word "dynamic" from the
American Heritage Dictionary.
dy·nam·ic - Characterized by continuous
change, activity, or progress.
As my wood art or studio
furniture is being handcrafted, sometimes the design I originally envisioned
can be improved at different stages, or the original design can remain as is.
Having this flexibility provides a continuous excitement for the wood artist or
studio furniture maker along with the benefit of improvising on the original
design after seeing the wood art at various intermediary stages. An excellent
example is the hall table design in my previous posts. I had chosen to invert
the base of the table for both aesthetic and technical reasons. Not to say the
original design of the maquette would not have worked, inverting it just
simplifies a design dilemma for me and introduces a new aesthetic to the piece.
After creating the maquette, I realize I needed to have a fairly stable, strong
sub-base to be able to support the V-shaped arch, whereas inverting the base
utilizes the points of the arches as legs.
Often, we become fixated
on a particular design and don't bother seeking out alternatives which often
stare us right in the face. Case in point, I have been creating a new design
for a smaller wood object, and as part of my philosophy I strive to use as many
materials in my possession as possible, without continuously sourcing new
material for the components. Working with material at hand sometimes limits
what I can do, but on the other hand challenges me to work within certain
constraints, in this case certain materials. So this would be an instance of what
I like to call "dynamic design". Sometimes the beauty of a design is
also in its simplicity. Simplicity is one of the tenets of the minimalism
philosophy. I must admit that I am a fan of "minimalism", and have
read at least one book on the subject. You tend to gain a different perspective on
design after being exposed to the philosophy of minimalism.
Tuesday, March 17, 2015
Design (2)
In my previous post I discuss the concept of hatching a design and transferring it to paper. I now have a sketch on a pad and need to evolve this sketch into an object. At this stage I begin to refine the design, since it is but a sketch at this point. The sketch now evolves into a drawing with more defined, straight and equidistant lines. This process involves a few iterations and I build from my previous drawing with each of the iterations. This process results in a drawing which closely resembles the wood object I wish to create. Although the shape of the object has been essentially defined, an important component of the design is yet to come. Many of my designs have the type of wood and the grain graphics of the wood as the focal point. I usually begin with the design and then select woods with interesting graphics. Graphics is another word for grain pattern and the mix of heartwood and sapwood on a board, which can be either pronounced or subdued. I then spend time determining how to incorporate this interesting wood into the design.
On occasion, I instead create a design around a particularly interesting board or set of boards which have exciting, interesting graphics. Basing a design around a particular board or set of boards can be quite challenging, and I like to rise to challenges. I find challenging myself expands my skills and provides me a different outlook on the design process. Instead of a methodical approach, it is instead "material based" for lack of a better set of words.
These are my two approaches to design. The first one involves drawing and refining a design and then acquiring a selection of woods to make the piece. The second approach involves having wood with interesting graphics and basing a design around this wood. This approach is more of an artistic approach to my craft, whereas the first approach I would say is the craftsman method. They both have their place and serve a purpose. I typically use the artistic approach for speculative work and use the more structured craftsman method for commissions where a design needs to be defined. Once the design is fairly complete and drawings ready, the technical details are determined. These details involve the dimensions of the individual pieces of wood, the joinery involved, is there any alternative media in the piece?
I get excited about finding a board or boards with interesting graphics and color and then creating an object with this wood. This must be the artist in me...
On occasion, I instead create a design around a particularly interesting board or set of boards which have exciting, interesting graphics. Basing a design around a particular board or set of boards can be quite challenging, and I like to rise to challenges. I find challenging myself expands my skills and provides me a different outlook on the design process. Instead of a methodical approach, it is instead "material based" for lack of a better set of words.
These are my two approaches to design. The first one involves drawing and refining a design and then acquiring a selection of woods to make the piece. The second approach involves having wood with interesting graphics and basing a design around this wood. This approach is more of an artistic approach to my craft, whereas the first approach I would say is the craftsman method. They both have their place and serve a purpose. I typically use the artistic approach for speculative work and use the more structured craftsman method for commissions where a design needs to be defined. Once the design is fairly complete and drawings ready, the technical details are determined. These details involve the dimensions of the individual pieces of wood, the joinery involved, is there any alternative media in the piece?
I get excited about finding a board or boards with interesting graphics and color and then creating an object with this wood. This must be the artist in me...
Sunday, March 15, 2015
Design...
When you are creating either a piece of furniture or a wood object and not following a pre-determined plan, a design will need to be established. I hardly ever work from plans. The design process typically begins with an idea hatched in my mind and is then transferred to a sketch pad. The idea might have originated from a shape I have seen, the need for a particular object or a furniture piece with certain design criteria, or simply an idea hatched on a whim. The basis of the design process is coming up with a good design. What is it about a design that make it a success? Is it the aesthetics of the piece, the pleasing proportions, the balance of form and function... or all these characteristics combined?
Taking a step back, the aesthetics and pleasing proportions are definitely at the forefront. I'm usually drawn to a piece of furniture or object that stands out with respect to the "look" of the piece. This one characteristic causes me to stop and further examine the piece by trying to understand what has drawn me to this particular design. This analysis aids my design process as I better understand what characteristics of an object or piece of furniture I am drawn to. We all have different styles of furniture that we are drawn to, but the common theme is good design. My favorite style of furniture is modern and contemporary. Typically even an admirer of period styles of furniture will stop at a well-designed modern piece of furniture to further analyze it.
We've all heard the saying that everything has already been discovered or invented. I have even heard of this saying applied to furniture design. After all, we're re-shaping the same objects over and over... adding curves, changing proportions, adding ornamentation, removing the ornamentation, using darker or lighter woods, utilizing curves, replacing curves with straight lines, utilizing thicker or thinner components, etc. It is easy to come to this conclusion, however, I regularly see new pieces of furniture or decorative wood objects that make me sit back and say "wow, that is an interesting, unique design".. or "that is a cool design, I wonder if it's been done before". In light of this, the boundaries of design are limitless, one just needs to think outside the box. Also, I feel that often using pre-existing styles as templates for a new design sometimes handicaps the designer, where the designer subconsciously has the existing style in mind and cannot get past it. Sometimes it is better to begin with a clean slate, in my case, hatch an idea then transfer it to pad and pencil and begin to sketch it without being influenced by pre-existing designs.
Taking a step back, the aesthetics and pleasing proportions are definitely at the forefront. I'm usually drawn to a piece of furniture or object that stands out with respect to the "look" of the piece. This one characteristic causes me to stop and further examine the piece by trying to understand what has drawn me to this particular design. This analysis aids my design process as I better understand what characteristics of an object or piece of furniture I am drawn to. We all have different styles of furniture that we are drawn to, but the common theme is good design. My favorite style of furniture is modern and contemporary. Typically even an admirer of period styles of furniture will stop at a well-designed modern piece of furniture to further analyze it.
We've all heard the saying that everything has already been discovered or invented. I have even heard of this saying applied to furniture design. After all, we're re-shaping the same objects over and over... adding curves, changing proportions, adding ornamentation, removing the ornamentation, using darker or lighter woods, utilizing curves, replacing curves with straight lines, utilizing thicker or thinner components, etc. It is easy to come to this conclusion, however, I regularly see new pieces of furniture or decorative wood objects that make me sit back and say "wow, that is an interesting, unique design".. or "that is a cool design, I wonder if it's been done before". In light of this, the boundaries of design are limitless, one just needs to think outside the box. Also, I feel that often using pre-existing styles as templates for a new design sometimes handicaps the designer, where the designer subconsciously has the existing style in mind and cannot get past it. Sometimes it is better to begin with a clean slate, in my case, hatch an idea then transfer it to pad and pencil and begin to sketch it without being influenced by pre-existing designs.
Friday, March 13, 2015
Scale models (maquettes)
The aXial Lounge Chair began as a sketch , drawings and a series of maquettes or scale models of the design. I typically sketch a design , then draw it either in pencil or through CAD software. This provides me the feasibility of the design... is it appealing? is it structurally sound? is it innovative? I work through the design process and flesh out the final design using an iterative process. The design needs to be elegant, aesthetically appealing and sometimes innovative.
In this case I introduced innovation into the aXial Lounge Chair through the X-pattern frame. Developing the design is an enjoyable process as I make an effort to reduce the number of components or finesse them while maintaining strength in the design. Chairs have a unique process since they need to endure different stresses as well as being aesthetically pleasing. You can see the progression in the size and detail of the scale models in the attached image. The next step is a full size scale model and drawing of the main components of the design. Full size drawings enable me to accurately create the components through repeatability.
In this case I introduced innovation into the aXial Lounge Chair through the X-pattern frame. Developing the design is an enjoyable process as I make an effort to reduce the number of components or finesse them while maintaining strength in the design. Chairs have a unique process since they need to endure different stresses as well as being aesthetically pleasing. You can see the progression in the size and detail of the scale models in the attached image. The next step is a full size scale model and drawing of the main components of the design. Full size drawings enable me to accurately create the components through repeatability.
Wednesday, March 11, 2015
New Ebook...
Upon my return from IDS15 in Toronto I needed a day or two to catch up on the many emails I received during my time away. I also had other business to tend to during the first few days of my return. Then a much needed break for a few days to recharge myself. I typically do this after an intensive period. IDS15 preparations and doing the actual show demanded considerable energy, so I feel I was entitled to a break afterwards.
The interesting part about these breaks is that it foster new ideas in my mind. I had nothing on my plate so to speak and this causes the ideas to flow. With a previous goal to publish an e-Book in mind, I decided to pursue this. Expanding on an earlier publication of mine; the result is my first e-Book with much more content and images. I am glad to share the topics and issues I have experienced in the startup of four woodworking related businesses. So the newly released Start Your Own Woodworking Business eBook is hot off the press and available through WoodSkills !
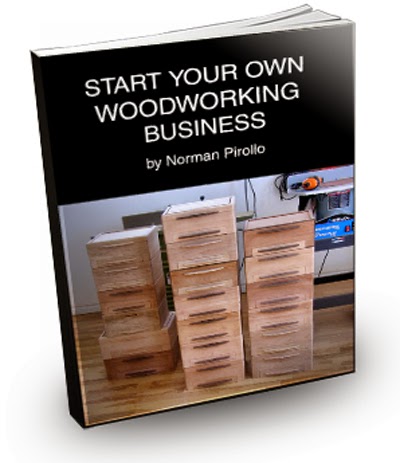
IDS15 Summary
After a hectic 5 days exhibiting at IDS15, I can say it was cool to be able to discuss my new chair design with so many people. The feedback and interest the lounge chair received was much higher than my expectations. The design is so new that I literally had no time before IDS15 to determine its wide acceptance. So IDS15 was it!
Everything went smoothly at the show. This is my second year exhibiting in the Studio North area of IDS15 so the anxiety level has diminished considerably. A considerable number of people sat on the chairs and their first words were usually ” it’s so comfortable”. Other comments include “the angles of the seat and back are great”, “the chair is not inclined too far back”, “seating is firm”, etc.
I had some very good news yesterday, so excited about where this will lead. Baron Magazine picked my aXial Lounge Chair as one of the Top 10 Product Designs at IDS15. Article with photos here:
IDS15 Studio North
Studio North..an area of IDS15 set aside for emerging Canadian designers. The exhibitors in this area are juried and I am excited to be a part of it. This is my second year in Studio North and I will be introducing the newly designed aXial lounge chair. Last year I introduced the Nuovo Console Tables. Have to say I truly enjoyed the experience and am looking forward to talk to fellow designers, the interior designer community and the public. The time flew at IDS14, I expect IDS15 to be a whirlwind time! Some marketing items I brought with me this year.Booth SN35 at the Metro Toronto Convention Center Jan 22-25. Follow me at Twitter @pirollodesign for show updates!
aXial Hi-back Lounge Chair
A glimpse of the new aXial Hi-back Lounge Chair I will be introducing at IDS15 in Toronto from Jan. 22-25. It is a contemporary styled hi-back lounge chair which features a unique X-pattern frame. The innovative X-pattern frame eliminates the need for rails and stretchers creating a modern aesthetic in a refined, sleek appearance. The Canadian designed + handcrafted aXial lounge chair will be available in a variety of woods including walnut, maple, birch, cherry and ash. Seat and back upholstery is available in selection of fabrics or top grain leather in a large selection of colors. Shown is a solid walnut chair with top grain white Italian leather seat and back.
Dimensions: 38 in. H x 27 in. D x 22 in. W
Lounge Chairs
I’ve been steadily working on the development of a new series of lounge chairs. These lounge chairs have unique design characteristics which have involved considerable design and development to get right. I am glad to say that the production version is currently having finish applied and I’m pleased with the design.
Design considerations such as rigidity, strength, ergonomic concerns, aesthetic criteria and contemporary design have all come together in this lounge chair. Early prototypes can be seen in this photo. The design has since evolved and become more refined. The series of prototypes were essentially mules to be able to test for optimum seating heights, depths, angle, etc.
Subscribe to:
Posts (Atom)